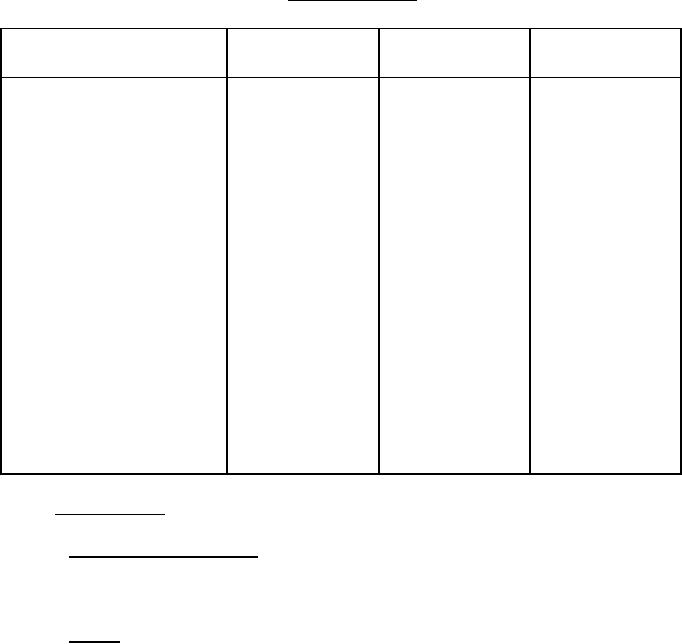
MIL-PRF-81733D
TABLE V. Qualification tests.- Cont'd
Test
Requirement
Test
Characteristic
Method
Paragraph
Paragraph
Tack-free time
3.3.1.6
4.8.5
Assembly time
3.3.1.7
4.8.6
Hardness
ASTM-D2240
3.3.2.1
4.8.7
Specific gravity
3.3.2.2
4.8.8
Corrosion
3.3.2.3
4.8.9
Low-temperature flexibility
3.3.2.4
4.8.10
Thermal stability
3.3.2.5
4.8.11
Tensile strength
ASTM-D412
3.3.2.6
4.8.12
Elongation
ASTM-D412
3.3.2.7
4.8.12
Peel strength
3.3.2.8
4.8.13
Anchorage (wet tape)
3.3.2.9
4.8.14
Repairability
3.3.2.10
4.8.15
Air content
3.3.2.11
4.8.16
Long-term storage
3.3.3
4.8.17
Unit of issue
3.2.2
Visual
Warning label
3.2.4
Visual
4.5 Test conditions.
4.5.1 Temperature and humidity. Unless otherwise specified, all mixing, curing,
conditioning, and testing shall be conducted at a temperature of 77° ± 5° F (25° ± 3° C) and a
relative humidity of 50 ± 5 percent. These conditions shall be considered standard conditions.
4.5.2 Mixing. The base compound and its curing agent, both in their original unopened
containers, and all required mixing equipment shall be held at standard conditions for 24 ± 1
hours. The base compound and curing agent shall then be thoroughly mixed in the proportions
recommended by the manufacturer. Proper care should be taken to avoid incorporation of air by
excessive stirring or folding action. Immediately after mixing, Type II sealing compound shall be
placed into cartridges for extrusion from the Semco No. 250 gun, or equivalent, having a Semco
440 nozzle with an orifice of 0.125 ± 0.005 inch.
11
For Parts Inquires call Parts Hangar, Inc (727) 493-0744
© Copyright 2015 Integrated Publishing, Inc.
A Service Disabled Veteran Owned Small Business