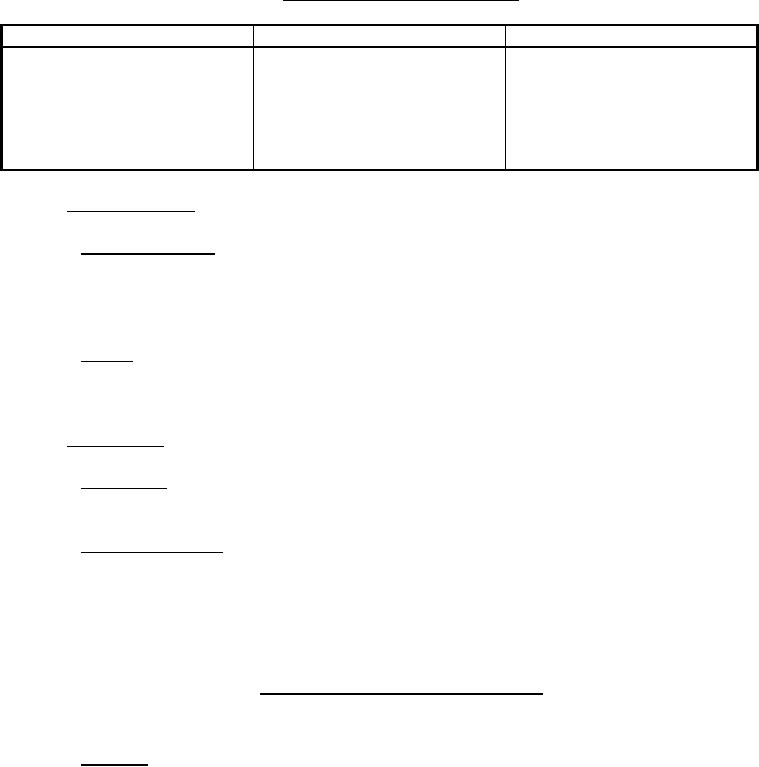
MIL-PRF-23586F
TABLE V. Formulation of test panel cleaner.
Ingredient
Specification
Percent By Volume
50.0 ±2.5
Aromatic petroleum naphtha
TT-N-97, type I, grade B
20.0 ±1.0
Ethyl acetate
TT-E-751
20.0 ±1.0
Methyl ethyl ketone
ASTM-D740
10.0 ±0.5
Isopropyl alcohol
TT-I-735
4.6 Curing conditions.
4.6.1 Classes 1, 2, and 3. All test specimens shall be cured at standard conditions (see 4.4.1)
for a maximum of 72 ±2 hours. All molded specimens shall be removed from the molds in 24 ±2
hours, and total cure time shall include the time the specimen is in the mold. Unless otherwise
specified, cured specimens shall be tested within 2 hours from the end of the cure period.
4.6.2 Class 4. Class 4 sealing compound shall be cured at 80° ±1°C (175° ±2°F) for 3 hours.
Cured specimens shall cool to standard conditions and be permitted to stand for 4 hours or more
after reaching standard conditions before testing.
4.7 Test methods.
4.7.1 Appearance. The sealing compound shall be visually examined for conformance to
3.3.1.1.
4.7.2 Nonvolatile content. Five to ten grams of the mixed sealing compound shall be
transferred to a dish approximately 8 centimeters in diameter. The weight shall be determined to
the nearest milligram. The compound shall be heated for 24 to 26 hours at 70° ±1°C (158° ±2°F),
transferred to a desiccator, cooled to standard conditions (see 4.4.1), and weighed to the nearest
milligram. The percent nonvolatile content shall be calculated as follows:
Final weight of mixed compound
Percent nonvolatile content =
X 100
Initial weight of mixed compound
4.7.3 Viscosity. The viscosity of the base compound shall be determined by a Brookfield
viscometer, or equivalent. In using the viscometer, the spindle and speed shall be consistent with
the viscosity of the material tested. All readings shall be taken after a minimum of 3 spindle
revolutions.
11
For Parts Inquires call Parts Hangar, Inc (727) 493-0744
© Copyright 2015 Integrated Publishing, Inc.
A Service Disabled Veteran Owned Small Business